Tire Model Selection
by Cliff Hodges
Heavy emphasis has been placed on vehicle simulations to improve the performance of handling, ride comfort, and safety, which are all customer focused areas and are required to comply with regulations. However, when it comes time to select the tire model to use and the facility to complete the testing, which one should you choose? Simply put, it depends on your vehicle model application, fidelity, and cost. In the end, every company must balance a relationship between the quality and cost of any given product, of which the goal is to find the highest return on investment. That being said, the tire model selection process uses this principle while factoring in the model’s intended application. Some commercially available tire models are MF-Tyre™, MF-Swift™, PAC2002, FTire™, and CDTire™. These models are widely known across the industry and are frequently used in the development of vehicle dynamics platforms.
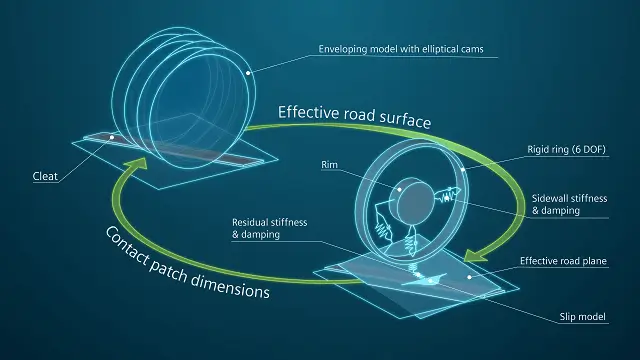
As we move through these models in detail, it is important to remember that there is not a one-size-fits-all method. Each one was designed with a specific purpose and intended outcome. MF-Tyre is the most commonly-used tire model due to its simplistic approach and modeling techniques. This is considered an empirical model, which simply means the tire’s physical structure is not attributed to the parameterization process. Advanced mathematical equations are used to fit force and moment response curves and output their coefficients. These values can then be input into vehicle simulation software to predict vehicle responses during maneuvers. MF-Tyre uses a single point contact tire model which oversimplifies the tire-road interaction being transmitted to a single contact point. MF-Tyre empirically describes the relationship between tire kinematics (as inputs) and tire steady-state force and moment (as outputs) assuming a flat road surface. MF-Tyre was specifically developed to predict handling performance. However, when technology and simulation platforms began evolving, tire models also evolved to include ride and comfort predictions as well. This led to the development of MF-Swift, an extension of MF-Tyre, which implements an enveloping model to predict the dynamic tire and surface interaction and couples it with MF-Tyre’s single point contact model. The MF-Swift model calculates vertical and longitudinal tire modes up to 100hz and is primarily used to analyze ride comfort, road load, and vibration phenomena. PAC2002 uses similar techniques as MF-Tyre and MF-Swift, being that the original formulation was created by the late Hans Pacejka. The biggest difference is that MF-Tyre is licensed by TNO, in conjunction with Siemens, and PAC2002 is licensed by MSC software. This separation of licenses has led to a difference in formulation relative to handling and ride comfort models, but both serve a similar purpose.
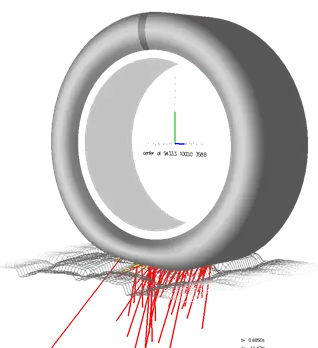
After discussing the methodology behind empirical models, the next tire models discussed will consider a physical approach to modeling the tire and road surface interaction. FTire, developed by Cosin Scientific Software, is another widely used tire model in the industry and offers advanced features with complex formulation methods. For instance, FTire is a physical tire model, meaning that the formulation of parameters is coupled, and directly correlated, with the physical structure of the tire. Based on physical test data, tire parameterization considers the structural makeup of the tire as well as the shear and strain forces applied during loaded applications. Essentially, this model separates the tire into numerous belt sections and captures the relationship between each section as it relates to the tire as a whole. FTire applies a flexible ring approach to the tire’s structure, which allows it to be unconstrained by single point contact limitations. In this flexible ring, a finite number of belt sections are connected by non-linear springs and bending stiffness in both in-plane and out-of-plane directions. Additionally, these methods used by FTire enable short and large-waved obstacle measurements to model the tire’s modal response up to 200hz. Unlike empirical models, parameters that directly correlate to the tire’s physical attributes must be adjusted to achieve accurate fit results, thus relying heavily on the engineer’s comprehension of tire mechanics and physics. This parameterization process, as just described, illustrates the complexity of these calculations and is consequently more time consuming than other tire models. FTire is compatible with most commercially available vehicle dynamics solvers and simulation platforms.
CDTire is another example of a physical tire model used in the automotive industry. This shell-based model uses multi-physics components such as mechanical, thermal, and cavity modeling. Mechanically, this model predicts large deformations and frictional contact under loaded conditions. Integrating two-dimensional tire CT scans, CDTire calculates the tire construction’s belt angles and uses them as a parameter to predict influence on force generation and structural integrity. Thermally, this model captures the structural effects of the heat propagation and the residual frictional effects on the tire’s surface interaction. One of CDTire’s most notable attributes to tire modeling is the ability to model the cavity mode during cleat impacts. The cavity model implements Euler’s ideal gas law theory, coupled with cleat impact response, to model the internal pressure cavity mode, generally above 200Hz.
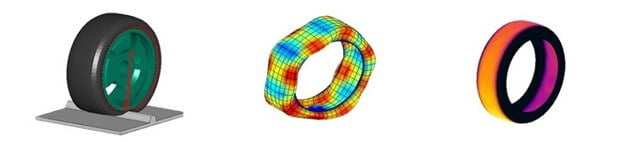
Additional tire models used in the industry include MegaRide™ and TameTire. MegaRide™ is a multi-physical, thermodynamic model which uses proprietary techniques to measure the tire’s thermal conductivity. This method is then coupled with force and moment data to model the thermal effects on the tire’s frictional properties. MegaRide™ models are compatible with many vehicle dynamics and real-time simulation platforms. TameTire was developed by Michelin and model fitting is currently only performed by Michelin. This thermomechanical model uses thermal input to predict force and moment output. A brush model is used to describe the mechanical interaction and assumes the tire is uniformed and running on a flat, dry surface. Through rubber properties such as the shear modulus and glass transition temperature, the tire’s stiffness, frictional properties, and heat generation can also be modeled.
With all these choices of tire models, selecting the best fit for your vehicle application can be a daunting task. Knowledge of the model theories can provide further insight to ease the burden. With GCAPS engineer’s knowledge of the tire model theories, vehicle simulation practices, and vehicle development processes, knowledge transfer can be accomplished during the decision process.
The final issue, which is of equal importance as model selection, is the test data acquisition and the procedures used to characterize the tire. GCAPS uses internally developed procedure methods aimed at improving the model’s fidelity. These procedures have been verified with the tire model developers. GCAPS test machine, an MTS made LTRe, is the world’s most capable flat belt machine and offers high force and moment measurements combined with highly dynamic positioning rates. These capabilities ensure and improve the robustness of these tire models by offering dynamic test data to properly characterize the tire’s response and match innovative vehicle maneuvers. All models say they are the best and encompass everything needed for simulation improvements, but practically speaking, it just depends on your company’s application. GCAPS offers both testing and modeling at the same facility, which will improve modeling results, shorten lead times, and reduce costs. Additionally, GCAPS simulation team has the experience and industry leading expertise to generate tire models that improve vehicle simulations and enhance the mobility industry.
For more information on tire testing and model generation, contact us at info@gcaps.net